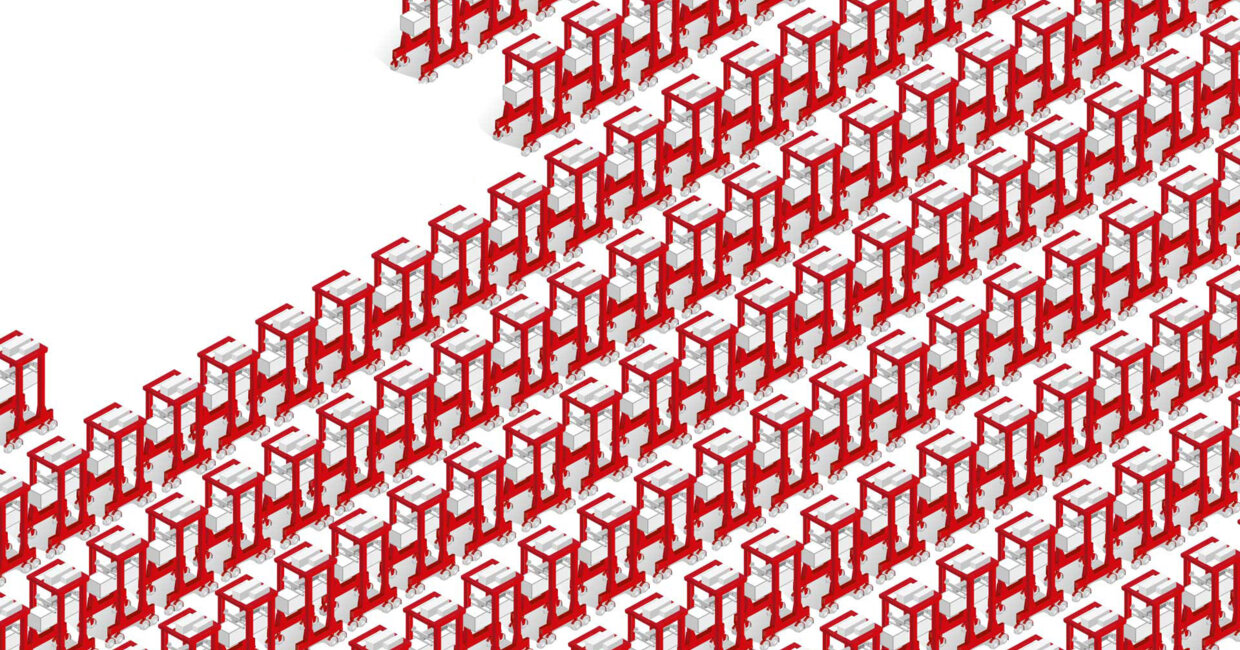
Over 300 Kalmar AutoStrad™ ordered globally to date
The Kalmar AutoStrad™ application is the industry-leading automated straddle carrier solution, with over 16 years of field-proven, highly successful operations around the world. Kalmar's entire range of straddle carriers can be factory equipped to be automation ready, and the solution enables terminals to automate their container handling operations at their own pace.
Available in stacking heights of up to 4 high, Kalmar AutoStrad™ make it possible for terminals to handle all their horizontal container transportation and stacking with a single type of machine. Kalmar AutoStrad™ are suitable for terminal and intermodal operations and can also be used to move containers between warehouses or depots as well as to and from the main yard.
"One of the great benefits of Kalmar AutoStrad™ is their flexibility," notes Tomi Tuulkari, Director, Product Management, Software and Automation Development, Kalmar. "AutoStrad™ can serve any type of yard or STS crane as well as road trucks, rail mounted gantry cranes and reefer racks. When combined with the capacity for 4-high stacking, this is really a game changer for our customers."
"One of the great benefits of AutoStrad™ is their flexibility,"
Proven track record
The history of Kalmar AutoStrad™ extends to the late 1990s, when the first automated straddle carriers were tested in industrial settings. The first fully automated AutoStrad™ terminal was the Patrick Container Terminal in Brisbane, which began operations with 27 machines in 2006. Since the introduction of the Kalmar AutoStrad™ system, Patrick’s AutoStrad™ terminal has become known as one of the safest in the world. Automated Straddle Carriers were subsequently introduced also at Patrick’s terminal in Sydney.
Today, over 300 Kalmar AutoStrad™ are in operation or being delivered at leading terminals around the world. These include six different locations around the globe with fleets from 130+ units to a smaller scale of 20+ machines.
"It is a testament to the reliability of the equipment that the original AutoStrad™ delivered to Patrick 16 years ago are still running strong, and are only now nearing the end of their lifecycle. This is considerably longer than the usual lifetime for manual straddle carriers," says Jarkko Mäkiranta, Director Automation Sales, Horizontal Transportation, Kalmar.
One-stop solution
With hundreds of units in everyday service around the world, the Kalmar AutoStrad™ application has been proven as a highly reliable, safe and competitive solution for ports and intermodal terminals. Automated Straddle Carriers support various levels of terminal and equipment automation and are compatible with both the Kalmar One terminal automation solution and other automation systems. Like Kalmar's other straddle carriers, Kalmar AutoStrad™ are available with multiple driveline options including hybrid and electric machines.
While other equipment manufacturers have offered automated straddle carriers, Kalmar is the only solution provider that has been able to automate all areas of container handling. "As a versatile and scalable solution, Automated Straddle Carriers are by far the most cost-effective solution for all terminals at which maximum stacking capacity is not the driving factor," says Hannes Myllarniemi, Sales Director & Sales Engineering, Kalmar. "When combined with fast deployment, a speedy return on investment and a superior safety record, Automated Straddle Carriers really do provide unparalleled operational flexibility. Not only can the solution be scaled depending on operational demands, but also the machines can easily be relocated if business needs or priorities change."
"While other equipment manufacturers have offered automated straddle carriers, Kalmar is the only solution provider that has been able to automate all areas of container handling."
Safe and predictable
AutoStrad™ and terminal automation help increase safety on multiple levels. Separating people from moving machines and omitting the human error factor from driving greatly reduce the risk of accidents. High safety standards ensure access to the yard when needed, and work ergonomy is improved by removing the need for drivers to work in difficult or dangerous conditions.
Alongside safety, the most common question from terminal operators concerning automated terminals is the difference in productivity between manual and automated operations.
"Manual terminals will produce the highest gross moves per hour but will have extremely high OPEX costs," says Jarkko Mäkiranta. "On average, automated terminals provide slightly fewer gross moves per hour, but offer more predictable 24/7/365 performance with significantly lower operating expenses. Partially and fully automated terminals will also require more focus on exception handling, but this impact can be greatly reduced by proper operational processes."
"Manual terminals will produce the highest gross moves per hour but will have extremely high OPEX costs."
DOWNLOADS
Related articles
Further reading
Subscribe and receive updates in your email
Unsere Veröffentlichungen abonnieren